Supply chain disruption is being felt across every industry. A recent study by McKinsey found that in most sectors, a single lengthened shock to production could wipe out up to half a year’s profits or more. And according to the National Association of Manufacturers, over 65% of respondents feel supply chain is a continual business challenge.
The key to resiliency is a long-term digital operations strategy focused on people, processes, and technology. And it’s a step manufacturers often miss. According to one Gartner study, only 30% of supply chain organizations feel their supply chain strategy is aligned with overall operational execution.
Now more than ever, supply chain resilience must be a top business priority.
What is a Resilient Supply Chain?
Resilient supply chains are those capable of adapting through constant disruption while also scaling to meet new demands. They are built on greater visibility and agility, allowing manufacturers to shift sourcing and distribution activities around as needed.
While Amazon continues to be the pinnacle of supply chain efficiency through its mastery of low levels of inventory, speedy delivery, and customer centricity, it’s not only behemoths that can command a resilient supply chain.
Take, for example, the story of a mid-sized west coast food product manufacturer whose agricultural supply chain began to centralize to the Midwest. New challenges, like longer transportation times and spoiled goods, forced them to reexamine their processes.
By tracing supply network from start to finish, the company identified weak points across the supply chain. By relocating, adding additional suppliers, and working on flexible in-house processes, the company ultimately eliminated one of their biggest supply chain issues. Now, with continuous monitoring of their data, they have been able to better monitor and forecast, increasing their agility and resiliency.
Five Ways to Build More Resilient Supply Chains
Inherent vulnerabilities exist in the way manufacturers operate. These vulnerabilities — such as the structure of the global supply chain, inadequate mapping, or a lack of business continuity planning, can trigger challenges when disruption occurs.
Here are five strategies to combat these vulnerabilities and adopt a more resilient supply chain network.
Achieve agility.
An agile supply chain refers to the ability to swiftly and responsively manage how a supply chain operates on a daily basis.
Having a solid understanding of the health and performance of your manufacturing process, even as the market fluctuates, will help you grasp your leading indicators. If you base your business decisions solely on lagging indicators, like revenue and purchase amounts, you won’t be able to achieve the flexibility necessary to innovate and grow with the market. Operational analytics can help you map out where you’re going and optimize your processes in order to meet future goals.
- A well-run supply chain lowers manufacturing costs, improves the reliability of deliveries, and helps you respond to unplanned demand.
Build visibility.
For many manufacturers, having real-time and actionable data throughout the entire manufacturing process is not a reality. Legacy systems and a lack of integration and data governance all equate to limited data visibility. In fact, only 6% of companies report having full visibility into their supply chain.
Manufacturers and supply chain leaders must accelerate technology adoption and prioritize data and analytics to gain visibility and foresight. This requires the implementation of big data and analytics with predictive and prescriptive analytics, enhanced data quality, and data capture.
For instance, using data to map your suppliers can prevent minor disruptions while also mitigating the effects of major ones. Trace your supply chain as far as you can to discover potential weaknesses now and into the future.
By systematically managing your data, you can gain consistent information throughout your supply chain planning and management process.
- Every company along the chain can benefit from greater visibility. Make your manufacturing company a data company.
Diversify and localize more of your supply.
Building resilience requires establishing relationships with multiple suppliers and manufacturers. More than 70% of supply chain leaders have already made changes to the size and number of locations in their supply chain network within the past two years. And 51% have increased the number of locations.
These findings illustrate the need to adapt networks to meet new market challenges. To secure your own supply chain, spread your procurement out so you’re not tied to just a few companies, especially for your most vital products and processes. You could have multiple suppliers of the same raw material so that, in a time of disruption, you can lean more on one than another.
Further, establishing cooperative relationships with multiple suppliers allows you to adjust your forecasts, orders, and increase sales more easily.
Standardization.
Standardized processes allow manufacturers to easily move production among plants, departments, or production lines to speed up recovery and improve real-time response.
This can entail everything from utilizing blockchain throughout your entire network of suppliers to standardizing your accounts payable processes.
To begin, make sure you align your procurement strategy with suppliers to create strong supplier network relationships. In addition, synchronize supply chain planning and execution, as well as how often you update your data and future company projections.
Digitizing processes.
Having the right supply chain technology in place and harnessing the power of your data can mean the difference for manufacturers facing disruptions.
Smart logistics solutions, the Internet of Things, robotics and artificial intelligence will all be key to future supply chain design according to the Association for Supply Chain Management’s supply chain transformation themes in 2023.
Digitizing operations unlocks real-time data that manufacturers can use to make decisions about production regardless of circumstance.
Building a More Resilient Supply Chain Begins with Planning
Supply chain disruption costs 45% of one year’s profits on average over the course of a decade.
In order to achieve the visibility, agility, and traceability necessary, organizations must begin to implement supply chain planning in their resiliency strategies. Every step in the supply chain process – from ordering raw materials to delivery – must be reliable.
Strategic, long-range supply chain planning involves the establishment of a framework for your supply chain. This includes a deep dive into your business and its suppliers with the goal of improving operations, standardizing processes, and planning for disruption.
Areas to review include:
- Demand planning
- Supply management
- Production management
- Inventory management
- Pricing strategy
- Event management
- Distribution planning
- Integrated business planning
By building resiliency strategies into every aspect of your operation, you’ll be better prepared to meet disruption and fluctuating market trends head on.
Digital transformation is key to the manufacturing entity of the future, as well as overcoming today’s challenges.
We're Here to Help
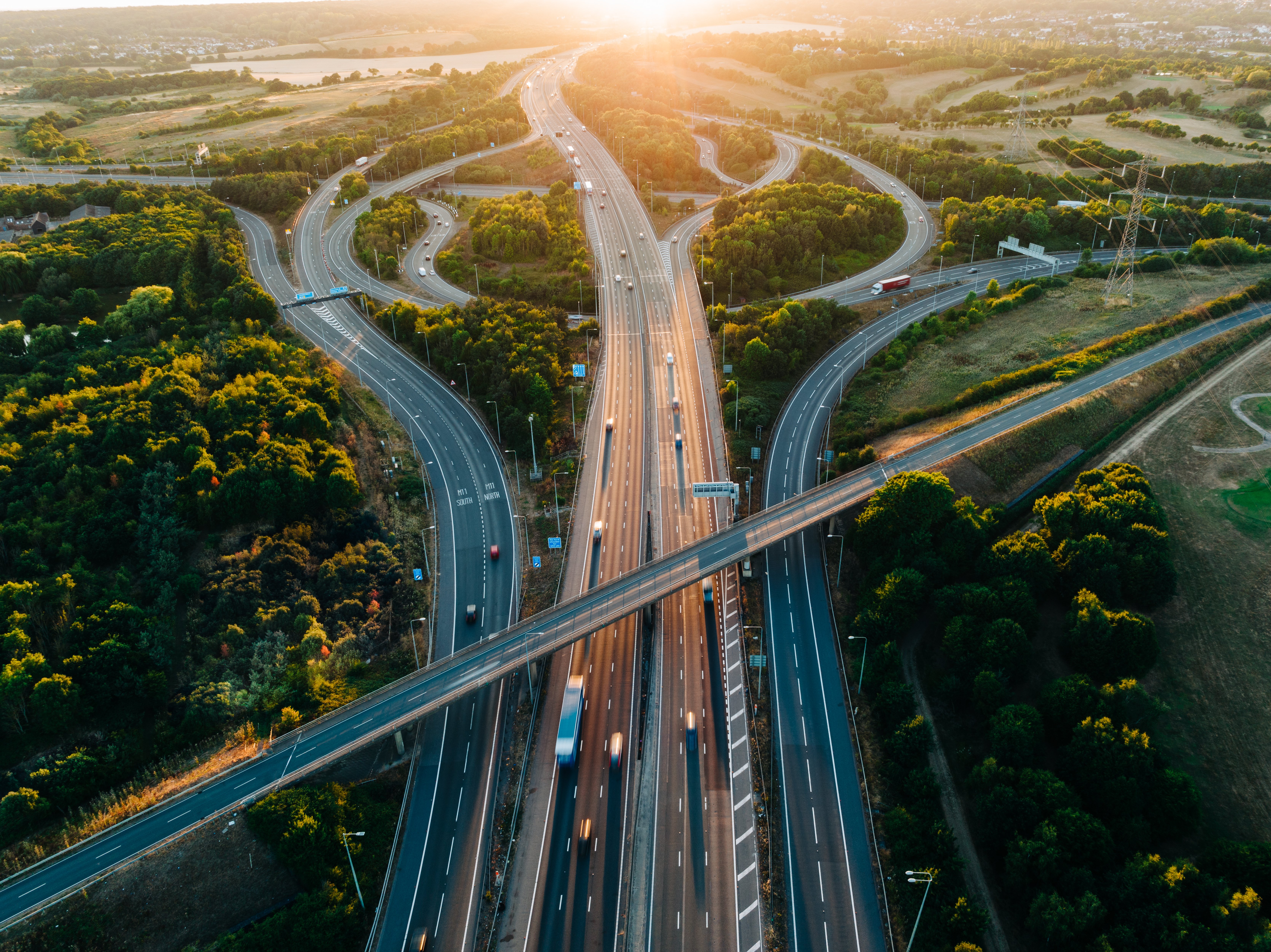